Project:
Large-diameter expansion joints for Metro Vancouver Wastewater Treatment Plan expansion
Overview: Metro Vancouver is undertaking a number of large-scale upgrades of its Annacis Island Waste Water Treatment Plant to meet the ever-growing needs of the Lower Mainland and provide protection for the facility in case of an earthquake.
Challenge: Metro Vancouver engineers identified the need for a wide range of expansion joints and equipment connection fittings to complete the WWTP expansion and earthquake-proof the facility.
Robar solution: Within the eight weeks requested by the Metro Vancouver project team, our staff and partners custom-made:
- A variety of fittings for pipes ranging from 3” – 88” diameters
- 28 expansion joints ranging from 54” – 88”
- 77 flexible expansion joints ranging from 3” – 42” pipe diameter
- 24 equipment connection fittings (12”)
Results: Working on a tight eight-week project timeline (competitors had estimated they would need four months to complete these pieces), Robar staff combined efforts with our partners, EBAA Iron and Baker Coupling, to produce these challenging, large-diameter products within timeframe and budget. Metro Vancouver’s project team appreciated the up-front support of Robar’s Sales team as well as the timely delivery of the custom-fit pieces.
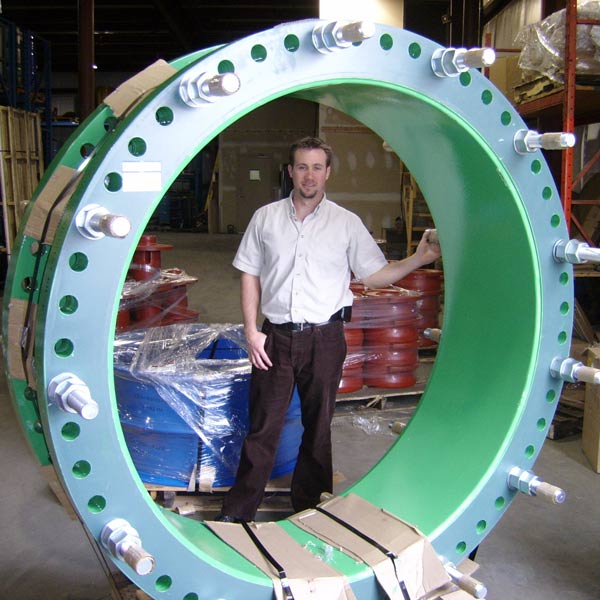
Project:
Large-diameter dismantling joints for Metro Vancouver
Overview: Metro Vancouver is undertaking a number of large-scale upgrades of its Annacis Island Waste Water Treatment Plant to meet the ever-growing needs of the Lower Mainland and provide protection for the facility in case of an earthquake.
Challenge: Metro Vancouver engineers identified the need for a wide range of expansion joints and equipment connection fittings to complete the WWTP expansion and earthquake-proof the facility.
Robar solution: With our ability to build dismantling joints (DJs) that can accommodate pipe sizes from 4” – 120” in diameter (and rated for high pressures), Robar was able to manufacture the 60” DJ to handle 300 PSI water pressure while still enabling the customer’s staff to adjust the fittings once the flange and other flanged fitting were in place.
Results: The flexibility provided by these DJs provided ease of installation of the new valve as well as ease of future maintenance with the ability to make repairs to their flanged piping system quickly and efficiently, saving thousands in the process.
Project:
Custom couplers designed, manufactured and installed for Saskatchewan potash mine
Overview: The potash mine required a flow meter installed on a brine pipeline for their potash mine.
Challenge: Maintenance staff could not completely stop the flow of brine through the pipe, a 32” metric HDPE DR17 brine pipeline, which eliminated butt fusion or electrofusion as possible options for this difficult process.
Robar solution: To meet the customer’s need, manufactured two mechanically restrained couplers c/w with stainless steel inserts (7946RFCAH 30D 31.59-.25×14 HDPE) and worked directly with the customer’s staff to field-measure the pipe, before determining the insert would need to be slightly enlarged to fit appropriately.
Results: With the flexibility of the Robar product, the insert was cut, expanded and welded in the field, avoiding a costly delay for the customer.
Project:
York Region concession road improvements
Overview: York Region required existing wastewater lines to be twinned to accommodate new developments in the region.
Challenge: The new lines needed to follow a relatively complicated route, under the Holland River Bridge and over railway tracks and an outdoor recreation area.
Robar solution: Working with AECON and Corix Water Products, this $94M project required a comprehensive plan for completing the twinning while mitigating the effects of the project from bridge and recreation area users. Key to this work was the manufacturing of 4 -1906RSCHH 36.00 ½ x 12 Restrained Couplings on DR 11 HDPE, designed to prevent pipe pull-out.
Results: The project involved a number of construction phases but wound up a success with Robar’s HDPE restrained playing a key role by tying the two pipelines together to complete the project.